核心实力 · 提供整体解决方案和全生命周期服务
集研发、生产、销售、售后为一体的综合性生产企业
厂区展示 · 展现企业雄厚实力
公司拥有30余年行业经验,技术实力雄厚
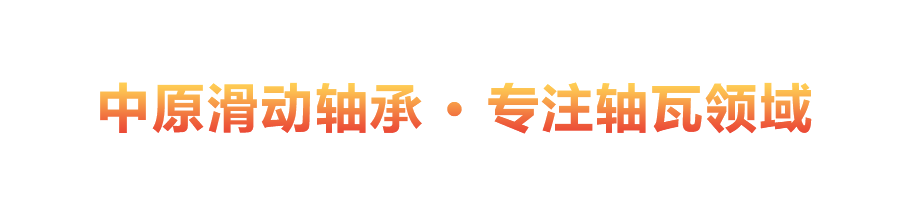
河南中原滑动轴承制造有限公司(原:新乡市中原轴瓦厂)是生产巴氏合金轴瓦的厂家。公司始建于1978年,坐落于华夏文明发源地黄河北岸的新乡。东临大广高速西接京珠高速交通便利。公司集研制、开发、生产、销售和服务为一体。配套设置齐全,工艺成熟,具有完善的质量保证体系和检测手段
【了解更多】OUR
STRENGTH
我们的实力
1978
公司成立时间
4000 +
企业年产值
80 +
在职员工
2000 +
累计服务客户
新闻中心 · 带你了解更多行业资讯
聚焦行业热点,时刻为您提供行业新动态
新动态襄盛举、绘蓝图、新跨越
襄盛举、绘蓝图、新跨越 —— 李总代表公司参加中通协压缩机分会第八届会员代表大会暨第四届压缩机产业发展年会 2021年 6月3日,以“襄盛举、绘蓝图、新跨跃”为主题的中国通用机械工业协会压缩机分会第八届会员代表大会暨第四届压缩机产业发展论坛在成都召开。李永磊总经理和李永超副总经理代表公司参加了大会。 中国通用机械工业协会秘书长孙放、中国通用机械工业协会压缩机分会理事长吴丰,秘书长姜大任,SEI***专家王存智,清华大学教授马凡华,西安交通大学教授彭学院、李云,华中科技大学教授张晓青等行业专家、协会会员企业负责人、委员会委员以及致力于行业发展的全产业链相关单位二百余位代表参加了会议。 会上多名专家教授就“碳达峰碳中和目标压缩机行业的发展机遇”、“中国发展氢能的思考和建议”、数值仿真应用于通用机械的机遇和挑战”“压缩机采购发展和趋势”等目前行业前沿科技议题进行了报告。国际形势以及科学技术的发展新趋势,对压缩机行业的发展是机遇也是挑战。作为压缩机行业的配套产品轴瓦,也要与时俱进,不断创新,才能跟上时代的脚步和行业的发展。 6月4日两位李总参观了森兰科技有限公司和中国石油集团济柴动力有限公司成都压缩机分公司,通过参观考察,我们不仅了解了**企业的管理优势,也意识到了我们自身的不足和差距。大力推进企业管理现代化、不断提升产品技术含量、加大科技研发力度将成为今后公司未来的工作重点。
2021-06-11
MORE+
01
1970-01
总经理致辞
我公司自2002年建立以来,承蒙各生产厂家和客户朋友鼎立相助,公司规模逐渐壮大,取得了较好的成绩。在此,我谨代表全体同仁发自内心地相各位致以深深的谢意! 常言道:十年修得同船渡。相逢是缘,相交更是缘。公司全体员工在这十余年的路途上,本着“与人方便,自己方便”的古训为人做事,时刻与各厂家和用户朋友亲密相处,精诚合作、风雨同舟、甘苦共享。我们深以与你们同行共渡为容!我们更看重和珍惜彼此间的事业和友情。 无论何时何地,我们全体员工都会不遗余力地投入到工作之中,竭尽所能为各位朋友提供满意的服务,以达到我们彼此的共赢和多赢。朋友们:闲时请来公司做客忙时电话短信问候。承蒙各生产厂家和客户朋友鼎立相助,公司规模逐渐壮大,取得了较好的成绩。在此,我谨代表全体同仁发自内心地相各位致以深深的谢意! 常言道:十年修得同船渡。相逢是缘,相交更是缘。公司全体员工在这十余年的路途上,本着“与人方便,自己方便”的古训为人做事,时刻与各厂家和用户朋友亲密相处,精诚合作、风雨同舟、甘苦共享。我们深以与你们同行共渡为容!我们更看重和珍惜彼此间的事业和友情。无论何时何地,我们全体员工都会不遗余力地投入到工作之中,竭尽所能为各位朋友提供满意的服务,以达到我们彼此的共赢和多赢。
朋友们:闲时请来公司做客忙时电话短信问候。
01
1970-01
质量目标
以顾客为关注焦点:组织依存于其顾客。因此组织应理解顾客当前和未来的需求,满足顾客并争取超越顾客期望。 领导作用:领导者确立本组织统一的宗旨和方向。他们应该创造并保持使员工能充分参与实现组织目标的内部环境。 全员参与:各级人员是组织之本,只有他们的充分参与,才能使他们的才干为组织获益。 过程方法:将相关的活动和资源作为过程进行管理,可以更高效地得到期望的结果。 管理的系统方法:识别、理解和管理作为体系的相互关联的过程,有助于组织实现其目标的效率和有效性。 持续改进:组织总体业绩的持续改进应是组织的一个永恒的目标。 基于事实的决策方法:有效决策是建立在数据和信息分析基础上。 互利的供方关系:组织与其供方是相互依存的,互利的关系可增强双方创造价值的能力。
01
1970-01
企业文化
为了实现我们的愿景,我们不断努力、超越自我、创造非凡、追求***。多元化的产品结构、多层次的知识更新、多地域的员工组合是公司执着的学习追求、不断超越自我、创造非凡、努力向上的价值观念的充分体现; 公司鼓励员工树立自信、迎接挑战,培养高度的进取精神、敏锐的思维能力、和谐的团队协作、刻苦的工作作风、充分实现自我价值,所有这一切,就是为了让我们想得更多,为社会、合作伙伴、客户做得更好! 为了实现我们的愿景,我们不断努力、超越自我、创造非凡、追求***。多元化的产品结构、多层次的知识更新、多地域的员工组合是公司执着的学习追求、不断超越自我、创造非凡、努力向上的价值观念的充分体现; 公司鼓励员工树立自信、迎接挑战,培养高度的进取精神、敏锐的思维能力、和谐的团队协作、刻苦的工作作风、充分实现自我价值,所有这一切,就是为了让我们想得更多,为社会、合作伙伴、客户做得更好!
01
1970-01
滑动轴承简介
(一)滑动轴承的材质 轴承合金(通称巴氏合金或白合金) 常用的滑动轴承材料有轴承合金(又叫巴氏合金或白合金)、耐磨铸铁、铜基和铝基合金、粉末冶金材料、塑料、橡胶、硬木和碳-石墨,聚四氟乙烯(PTFE)、改性聚甲醛(POM)、等。 轴承合金是锡、铅、锑、铜的合金,它以锡或铅作基本,其内含有锑锡(Sb-Sn)或铜锡(Cu-Sn)的硬晶粒。硬晶粒起抗磨作用,软基体则增加材料的塑性。轴承合金的弹性磨量和弹性极限都很低,在所有轴承材料中,它的嵌入性及摩擦顺应性**好,很容易和轴颈磨合,也不易与轴颈发生咬粘。但轴承合金的强度很低,不能单独制作轴瓦,只能贴附在青铜、钢或铸铁轴瓦上作轴承衬。轴承合金适用于重载、中高速场合,价格较贵。 (二)滚动轴承与滑动轴承的区别 滚动轴承和滑动轴承的区别**表象在结构上,滚动轴承是靠滚动体的转动来支撑转动轴的,因而接触部位是一个点,滚动体越多,接触点就越多;滑动轴承是靠平滑的面来支撑转动轴的,因而接触部位是一个面。其次是运动方式不同,滚动轴承的运动方式是滚动;滑动轴承的运动方式是滑动,因而摩擦形势上也就完全不相同。 滑动轴承,在滑动摩擦下工作的轴承。滑动轴承工作平稳、可靠、无噪声。在液体润滑条件下,滑动表面被润滑油分开而不发生直接接触,还可以大大减小摩擦损失和表面磨损,油膜还具有一定的吸振能力。但起动摩擦阻力较大。轴被轴承支承的部分称为轴颈,与轴颈相配的零件称为轴瓦。为了改善轴瓦表面的摩擦性质而在其内表面上浇铸的减摩材料层称为轴承衬。轴瓦和轴承衬的材料统称为滑动轴承材料。 滑动轴承工作时,轴瓦与转轴之间要求有一层很薄的油膜起润滑作用。如果由于润滑不良,轴瓦与转轴之间就存在直接的摩擦,摩擦会产生很高的温度,虽然轴瓦是由于特殊的耐高温合金材料制成,但发生直接摩擦产生的高温仍然足于将轴瓦烧坏。轴瓦还可能由于负荷过大、温度过高、润滑油存在杂质或黏度异常等因素造成烧瓦。烧瓦后滑动轴承就损坏了。 所谓刮轴瓦,就是将精车后的瓦片与所装配的轴研合(轴要涂上色粉),用三角刮刀刮去瓦片上所附上的粉色,随研随刮,直到瓦片上附色面积超过全瓦面的85%,完成刮瓦。瓦片上存在的刀痕是瓦片储存润滑油的微型储槽。 (三)剖分式滑动轴承的装配(轴瓦装配) 剖分式向心滑动轴承,主要用在重载大中型机器上,如冶金矿山机械,大型发电机,球磨机,活塞式压缩机及大型风机等。其材料主要为巴氏合金,少数情况下采用铜基轴承合金(如回转窑等)。在装配时,一般都采用刮削的方法来达到其精度要求,保证其使用性能。因此,刮削的质量对设备的运转至关重要。削刮质量不好,设备在试车时就会很容易地在极短的时间内是轴瓦由局部粘损而达到大部分粘损,直至轴被粘着咬死,轴瓦损坏不能使用。所以在刮削轴瓦时都由技术经验丰富的钳工操作。 下面详细介滑动轴承(轴瓦)的装配要求及削刮轴瓦的方法。 1、轴瓦与瓦座和瓦盖的接触要求 (1)受力轴瓦。受力轴瓦的瓦背与瓦座的接触面积应大于70%,且应分布均匀。 (2)不受力轴瓦与瓦盖的接触面积应大于60%,且应分布均匀。 (3)如达不到上述要求,应以瓦座与瓦盖为基准,用着色法,涂以红丹粉检查接触情况,用细锉或油石对瓦背进行修研,直到达到要求为止。接触斑点达到每25mm23~4点即可。 (4)轴瓦与瓦座、瓦盖装配时,固定滑动轴承的固定销(或螺钉)端头应埋入轴承体内2~3mm,两半瓦合缝处垫片应与瓦口面的形状相同,其宽度应小于轴承内侧1mm,垫片应平整无棱刺,瓦口两端垫片厚度应一致。瓦座、瓦盖的连接螺栓应紧固而受力均匀。所有件应清洗干净。 2、轴瓦刮削面使用性能要求的几大要素 (1)油线与瓦口油槽带 a、半开式滑动轴承,都是采用强力润滑,油槽一般都开在不受力的上瓦上(上瓦受力较小)。截面为半圆弧形,沿上瓦内周180°分布,由机械加工而成。油槽中间位置与上瓦中心位置的油孔相通,两端连接瓦口油槽带,由于上瓦有间隙量存在,润滑油很容易进入上瓦面与轴上,其主要作用是能将润滑油畅通地注入轴瓦内侧(径向)的瓦口油槽带。 b、油槽带分布在上、下轴瓦结合部位处(两侧)。油槽带成圆弧楔形,瓦口结合面处向外侧深度一般在1~3mm。视轴瓦的大小,油槽带宽度一般为8~40mm。油槽带单边距轴瓦端面的尺寸一般为8~25mm。上述要求通常在图纸上明确标出。油槽带的长度为轴瓦轴向长度的85%左右,是一个能存较大量的润滑油的带状油槽,便于轴瓦与轴的润滑与冷却,油槽带通常由机械加工而成,也有钳工手工加工的。 (2)润滑油楔。润滑油楔位于接触范围角a值之内油槽带与轴瓦的连接处,由手工刮削而成(俗称刮瓦口)。其主要作用有两个,一是存油冷却轴瓦与轴,二是利用其圆弧楔角,在轴旋转的带动下,将润滑油,由轴向宽度的面,连接不断地带向承载部分,使轴瓦与轴有充分良好的润滑。润滑油楔部分是由两段不规则的圆弧组成的一个圆弧楔角,它将油槽带和轴瓦工作接触面光滑地连接起来。与油槽带连接部分要刮得多一些,并将油槽带连接处加工棱角刮掉,在润滑楔角中部至接触面过渡处,刮成圆弧楔角形。油槽带与润滑楔角连接处尺寸,视轴瓦的大小,一般在0.10~0.40mm之间。刮削润滑楔角,要在轴瓦精刮基本结束时进行,不易提前刮削。 (3)轴瓦的顶间隙与侧间隙 a、轴瓦的顶间隙,在图纸无规定时,根据经验可取轴直径的1‰~2‰,应按转速。载荷和润滑油粘度在这个范围内选择。对高质量、高精度加工的轴颈,其值可降到0.5‰。 b、侧间隙在图纸上无规定时,每面为顶间隙的1/2。侧间隙需根据需要刮削出来。但在刮削轴瓦时不可留侧间隙,因刮轴瓦时,需确定轴在180°范围内的正确位置,此时需有侧间隙的部位应暂时作为轴的定位用,要在轴瓦基本刮削完毕时,将侧间隙轻轻刮出。侧隙部位由瓦口的结合面处延伸到规定的工作接触角度区,轴向与油槽带、润滑楔角相接,此部位是不应与轴有接触的,刮削时应注意这点。留侧隙的目的,是为了散失热量,润滑油由此流出一部分并将热量带走。侧隙不可开得过大,这样会使润滑油大量地从侧隙流走而减少轴与轴瓦所需用的润滑油量,这点应特别注意。 3、剖分式轴瓦的刮削过程 (1)粗刮轴瓦。**将新的上、下瓦合在一起,用内径千分尺测量内径与轴颈进行比较,确定粗刮量。 a上、下瓦的机械加工刀痕轻刮一遍,要求瓦面应全部刮到,刮削均匀,将加工痕迹刮掉。 b轴上涂色,与上瓦、下瓦研点粗刮几遍,然后将上、下瓦分别镶入瓦座与瓦盖上,瓦上涂色,用轴研点粗刮,待接触面积与研点分布均匀后,可转入细刮。粗刮时应注意,不可将瓦口部分刮大了,要求180°范围全面接触。 (2)细刮轴瓦。细刮轴瓦时,上、下瓦应加垫(瓦口结合面)装配后刮削两端轴瓦,在瓦上涂色,用轴研点。开始压紧装配时,压紧力应均匀,轴不要压得过紧,能转动即可,随刮随撤垫,随压紧。此时也应注意不要将瓦口刮亏了,经多次削刮后,瓦接触面斑点分布均匀、较密即可。 (3)精刮轴瓦。精刮的目的是要将接触斑点及接触面积刮削达到图纸规定的要求,研点方法与粗刮相同,点子由大到小,由深到浅,由疏到密,大的点子在削刮过程中,可用刮刀破开变成密集的小点子,经过多次削刮,逐渐刮至要求为止。在精刮将要结束时,将润滑油楔(开瓦口)、侧间隙刮削出来,使其达到轴瓦的使用性能,这一点非常重要。 削刮轴瓦,在粗刮与细刮时要同时考虑与轴相关的尺寸情况,如中心距偏差、齿轮齿面的接触状况等,以便使轴的位置准确。由机械加工造成的微小积累误差,可通过刮削得到进一步的消除。较大误差,刮削是无法解决的。 (四)滑动轴承刮研的技术要求 1、基本要求 既要使轴颈与滑动轴承均匀细密接触,又要有一定的配合间隙。 2、接触角 是指轴颈与滑动轴承的接触面所对的圆心角。 接触角不可太大也不可太小。接触角太小会使滑动轴承压强增加,严重时会使滑动轴承产生较大的变形,加速磨损,缩短使用寿命;接触角太大,会影响油膜的形成,得不到良好的液体润滑。 试验研究表明,滑动轴承接触角的极限是120°。当滑动轴承磨损到这一接触角时,液体润滑就要破坏。因此在不影响滑动轴承受压条件的前提下,接触角愈小愈好。 从摩擦力矩的理论分析,当接触角为60°时,摩擦力矩**小,因此建议,对转速高于500r/min的滑动轴承,接触角采用60°,转速低于500r/min的滑动轴承,接触角可以采用90°,也可以采用60°。 3、接触点 轴颈与滑动轴承表面的实际接触情况,可用单位面积上的实际接触点数来表示。接触点愈多、愈细、愈均匀,表示滑动轴承刮研的愈好,反之,则表示滑动轴承刮研的不好。一般说来接触点愈细密愈多,刮研难度也愈大。生产中应根据滑动轴承的性能和工作条件来确定接触点。 如何进行轴承与轴配合的检测 轴承与轴的配合间隙必须合适,径向间隙的检测可采用下列方法。 1、塞尺检测法 对于直径较大的轴承,间隙较大,宜用较窄的塞尺直接检测。对于直径较小的轴承,间隙较小,不便用塞尺测量,但轴承的侧隙,必须用厚度适当的塞尺测量。 2、压铅检测法 用压铅法检测轴承间隙较用塞尺检测准确,但较费事。检测所用的铅丝应当柔软,直径不宜太大或太小,**理想的直径为间隙的1.5~2倍,实际工作中通常用软铅丝进行检测。 检测时,先把轴承盖打开,选用适当直径的铅丝,将其截成15~40毫米长的小段,放在轴颈上及上下轴承分界面处,盖上轴承盖,按规定扭矩拧紧固定螺栓,然后再拧松螺栓。取下轴承盖,用千分尺检测压扁的铅丝厚度,求出轴承顶间隙的平均值。 若顶隙太小,可在上、下瓦结合面上加垫。若太大,则减垫、刮研或重新浇瓦。 轴瓦紧力的调整:为了防止轴瓦在工作过程中可能发生的转动和轴向移动,除了配合过盈和止动零件外,轴瓦还必须用轴承盖来压紧,测量方法与测顶隙方法一样,测出软铅丝厚度外,可用计算出轴瓦紧力(用轴瓦压缩后的弹性变形量来表示) 一般轴瓦压紧力在0.02~0.04毫米。如果压紧力不符合标准,则可用增减轴承与轴承座接合面处的垫片厚度的方法来调整,瓦背不许加垫。 滑动轴承除了要保证径向间隙以外,还应该保证轴向间隙。检测轴向间隙时,将轴移至一个极端位置,然后用塞尺或百分表测量轴从一个极端位置至另一个极端位置的窜动量即轴向间隙。 当滑动轴承的间隙不符合规定时,应进行调整。对开式轴承经常采用垫片调整径向间隙(顶间隙)。
01
1970-01
剖分式滑动轴承的装配(轴瓦装配)
剖分式向心滑动轴承,主要用在重载大中型机器上,如冶金矿山机械,大型发电机,球磨机,活塞式压缩机及运输车辆等。其材料主要为巴氏合金,少数情况下采用铜基轴承合金。在装配时,一般都采用刮削的方法来达到其精度要求,保证其使用性能。因此,刮削的质量对机器的运转至关重要。削刮质量不好,机器在试车时就会很容易地在极短的时间内是轴瓦由局部粘损而达到大部分粘损,直至轴被粘着咬死,轴瓦损坏不能使用。所以在刮削轴瓦时都由技术经验丰富的钳工操作。下面详细介绍泵房式滑动轴承(轴瓦)的装配要求及削刮轴瓦的方法。 1、轴瓦与瓦座和瓦盖的接触要求 (1)受力轴瓦。受力轴瓦的瓦背与瓦座的接触面积应大于70%,而且分布均匀,其接触范围角a应大于150
°,其余允许有间隙部分的间隙b不大于0.05mm。如图1所示。 (2)不受力轴瓦与瓦盖的接触面积应大于60%,而且分布均匀,其接触范围角a应大于120°,允许有间隙部位的间隙量b,应不大于0.05mm。如图1所示。 图一轴瓦与瓦座、瓦盖的接触要求 (3)如达不到上述要求,应以瓦座与瓦盖为基准,用着色法,涂以红丹粉检查接触情况,用细锉锉削瓦背进行修研,直到达到要求为止。接触斑点达到每25mm23~4点即可。 (4)轴瓦与瓦座、瓦盖装配时,固定滑动轴承的固定销(或螺钉)端头应埋入轴承体内2~3mm,两半瓦合缝处垫片应与瓦口面的形状相同,其宽度应小于轴承内侧1mm,垫片应平整无棱刺,瓦口两端垫片厚度应一致。瓦座、瓦盖的连接螺栓应紧固而受力均匀。所有件应清洗干净。 2、轴瓦刮削面使用性能要求的几大要素 (1)接触范围角a与接触面、接触斑点要求。轴瓦的接触范围角a与接触面要求见表1。 表1轴瓦的接触范围角a与接触面要求 在特殊情况下,接触范围角a也有要求为60°的。对于接触范围角a的大小和接触斑点要求,通常由图样明确地给出。如无标注,也无技术文件要求的,可通用技术标准规定执行。(参照表1)轴瓦的接触斑点要求,可参照表2中数值要求,对轴瓦进行刮削和检验。 表2滑动轴承的研点数 (2)油线与瓦口油槽带 a、半开式滑动轴承,都是采用强力润滑,油槽一般都开在不受力的上瓦上(上瓦受力较小)。截面为半圆弧形,沿上瓦内周180°分布,由机械加工而成。油槽中间位置与上瓦中心位置的油孔相通,两端连接瓦口油槽带,由于上瓦有间隙量存在,润滑油很容易进入上瓦面与轴上,其主要作用是能将润滑油畅通地注入轴瓦内侧(径向)的瓦口油槽带。 b、油槽带分布在上、下轴瓦结合部位处(两侧)。如图2所示。油槽带成圆弧楔形,瓦口结合面处向外侧深度一般在1~3mm。视轴瓦的大小,油槽带宽度h一般为8~40mm。油槽带单边距轴瓦端面的尺寸b一般为8~25mm。上述要求通常在图样上明确标出。油槽带的长度为轴瓦轴向长度的85%左右,是一个能存较大量的润滑油的带状油槽,便于轴瓦与轴的润滑与冷却,油槽带通常由机械加工而成,也有钳工手工加工的。 图二轴瓦的油槽带与润滑油楔分布 (3)润滑油楔。润滑油楔位于接触范围角a值之内油槽带与轴瓦的连接处,由手工刮削而成(俗称刮瓦口)。其主要作用有两个,一是存油冷却轴瓦与轴,二是利用其圆弧楔角,在轴旋转的带动下,将润滑油,由轴向宽度的面,连接不断地吸向承载部分,使轴瓦与轴有充分良好的润滑。润滑油楔部分是由两段不规则的圆弧组成的一个圆弧楔角,它将油槽带和轴瓦工作接触面光滑地连接起来,其形状如图3所示。与油槽带连接部分要刮得多一些,并将油槽带连接处加工棱角刮掉,在润滑楔角中部至接触面过渡处,刮成圆弧楔角形。图中b的尺寸为油槽带与润滑楔角连接处尺寸,视轴瓦的大小,一般在0.10~0.40mm之间。刮削润滑楔角,要在轴瓦精刮基本结束时进行,不易提前刮削。 图三润滑楔角示意图 (4)轴瓦的顶间隙与侧间隙 a、轴瓦的顶间隙,在图样无规定时,根据经验可取轴直径的1‰~2‰,应按转速。载荷和润滑油粘度在这个范围内选择。对高质量。高精度加工的轴颈,其值可降到5/10000。 b、侧间隙在图样上无规定时,每面为顶间隙的1/2。侧间隙需根据需要刮削出来。但在刮削轴瓦时不可留侧间隙,因刮轴瓦时,需确定轴在180°范围内的正确位置,此时需有侧间隙的部位应暂时作为轴的定位用,要在轴瓦基本刮削完毕时,将侧间隙轻轻刮出。侧隙部位由瓦口的结合面处延伸到规定的工作接触角度区,轴向与油槽带、润滑楔角相接,此部位是不应与轴有接触的,刮削时应注意这点。留侧隙的目的,是为了散失热量,润滑油由此流出一部分并将热量带走。侧隙不可开得过大,这样会使润滑油大量地从侧隙流走而减少轴与轴瓦所需用的润滑油量,这点应特别注意。侧隙如图4所示,**宽处b为瓦口计划面处,尺寸为规定侧间隙的**大值。侧隙与瓦口平面处的尖角应倒角,视轴瓦大小,一般为1×45°~3×45°。侧隙基本上是由两段不规则的圆弧组成的。 图四侧间隙示意图 3、分式轴瓦的刮削过程 (1)粗刮轴瓦。如图5a所示 图5剖分式滑动轴承(轴瓦)的刮削 a上、下瓦的机械加工刀痕轻刮一遍,要求瓦面应全部刮到,刮削均匀,将加工痕迹刮掉。 b轴上涂色,与上瓦、下瓦研点粗刮几遍,然后将上、下瓦分别镶入瓦座与瓦盖上,瓦上涂色,用轴研点粗刮,待接触面积与研点分布均匀后,可转入细刮。粗刮时应注意,不可将瓦口部分刮亏了,要求180°范围全面接触。 (2)细刮轴瓦。如图5b所示。细刮轴瓦时,上、下瓦应加垫(瓦口结合面)装配后刮削两端轴瓦,在瓦上涂色,用轴研点。开始压紧装配时,压紧力应均匀,轴不要压得过紧,能转动即可,随刮随撤垫,随压紧。此时也应注意不要将瓦口刮亏了,经多次削刮后,瓦接触面斑点分布均匀、较密即可。 (3)精刮轴瓦。如图5c所示。加精刮的目的是要将接触斑点及接触面积刮削达到图样规定的要求,研点方法与粗刮相同,点子由大到小,由深到浅,由疏到密,大的点子在削刮过程中,可用刮刀破开变成密集的小点子,经过多次削刮,逐渐刮至要求为止。在精刮将要结束时,将润滑油楔(开瓦口)、侧间隙刮削出来,使其达到轴瓦的使用性能,这一点非常重要。 削刮轴瓦,在粗刮与细刮时要同时考虑与轴相关件的情况,如中心距偏差、步轮齿面的接触状况等,以便使轴的位置准确。由机械加工造成的微小积累误差,可通过刮削得到进一步的消除。较大误差,刮削是无法解决的。
01
1970-01
巴氏合金轴瓦的静止浇注法和离心浇注法
巴氏合金经常会被用来作为产品的表面材料,比如巴氏合金轴瓦就是以此作为材料,经过相应的加工工艺制成,这么设计的目的是为了提高整个轴瓦的耐磨性。通常情况下,巴氏合金轴瓦都会以浇注的方式成型,常用的有离心浇注和静止浇注两种。 既然称之为静止浇注法,那整个工艺基本处理静止的状态,先是根据轴瓦的具体尺寸选择适合的工装产品。然后在洁净、干燥的平台上准备好已经经过预热的石棉板,并且快速的将检查合格的轴瓦平放在上面,并且使其整个下端面与石棉板完全接触,目的是避免跑火。 紧接着要做的是将热加工的金属芯放入待浇注的轴瓦内,并通过找正的方式轴瓦的内圆与金属芯的外圆间隙均匀一致,同时要有足够的加工余量。浇注时,金属液流要呈现短而均匀的状态,才可以连续地沿胎具圆周移动。 从以往的操作经验来看,尽量是用预热过的搅拌棒进行搅动,促进合金液中的杂质、气体排除。当轴承合金全部浇入后,就可以进入到冷却环节;合金完全凝固就可以拆除胎具了,巴氏合金轴瓦也就成型了。 而巴氏合金轴瓦的离心浇注法过程中需要用到离心机和其他辅助设备,为了保证作业效果,需要事先检查设备的正常性,合格之后才能将轴瓦用预热过的夹具放置在主、从动夹盘之间,并用螺栓紧固在离心机上。 整个过程中要注意控制的是浇注温度和离心机的速度,等到浇注合金完全倒入后,才可以向轴瓦外表面喷水冷却,温度下降到一定值的时候才可以将巴氏合金轴瓦卸下。